食品企业人为管控VS信息化记录管控的对比
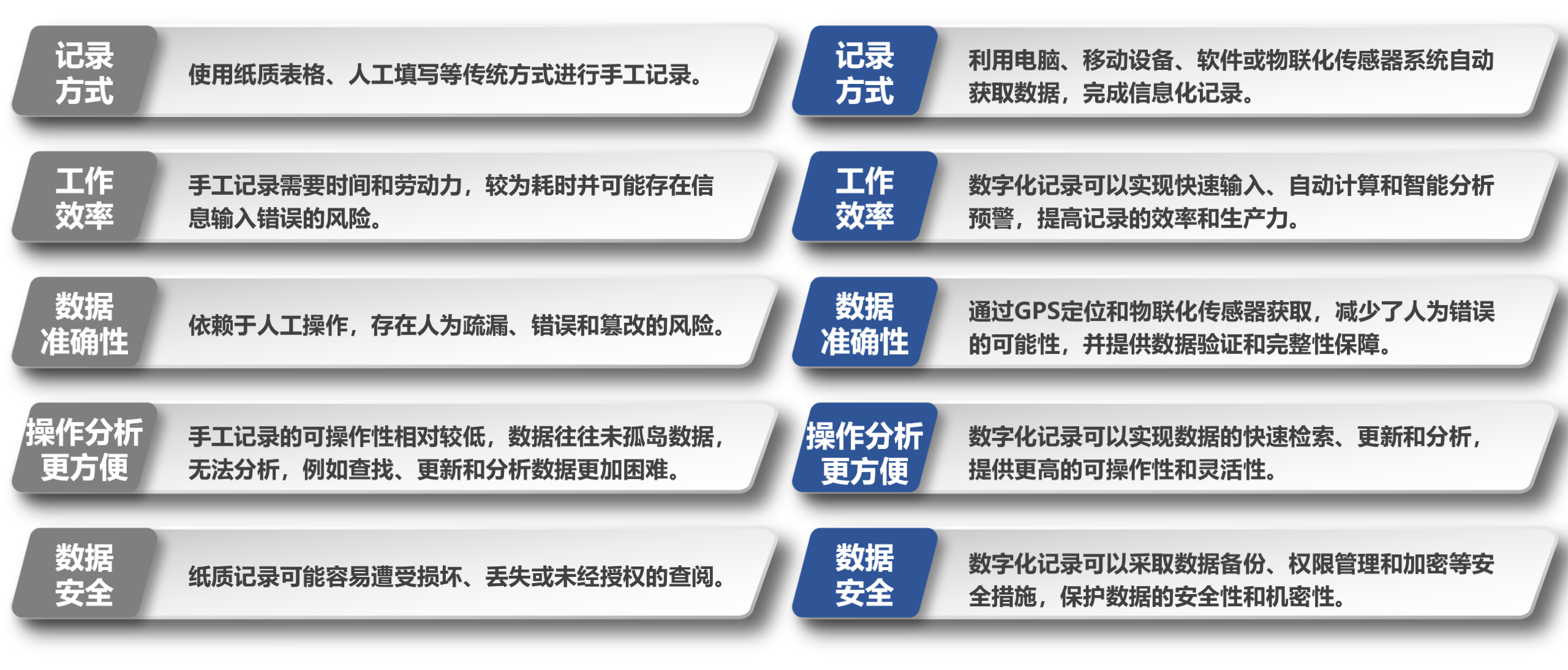
通过对客户传统产线的专业HACCP原则增设物联化传感器和控制元件,数字化地监测、预警和调控工艺参数,使生产线稳定精准的运行,低成本实现产品生产过程自动化监测与控制改造升级,提高产品合格率,生产过程数字化可追溯,问题批次原因可查,经验可量化,逐步实现过程控制产品合格100%。
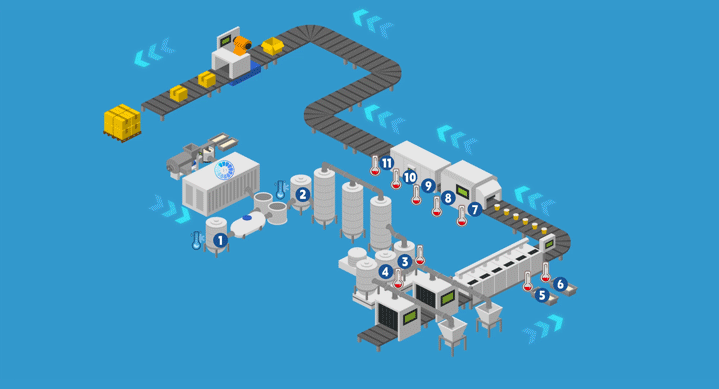
数字化生产线
提高产品合格率:
- 利用数字化系统和传感器,实时收集和监测生产过程中的关键数据,如温度、湿度、pH值等,发现异常实时预警,便于管理人员实时纠偏提升产品的合格率;
- 使用数据分析工具和联动各环节数据进行对比,识别潜在的质量问题,并及时采取纠正措施,例如:不同环节的存放时间、环境温度、湿度,综合在一起可造成产品的原始带菌量增高,使产品合格率降低;
- 通过数字化系统,建立供应链的可追溯性,包括原材料的来源、采购记录、生产过程数据等,便于记录不同批次生产的产品合格率情况,有利于最终确定原辅料的供应链;
- 员工因人为因素导致的产品摆放问题、转运问题,可通过可视化的信息记录暴露在管理人员面前,便于及时调整生产标准工艺规范,提高产品合格率;
提高生产效率:
- 利用数字化系统,对生产过程进行有效的记录,省去繁琐的纸质重复记录,有效的提高人员在数据采集过程中耗费的时间;
- 通过物联化设备对生产过程进行数据采集,可实现人员实现远程监控和管理;
- 资证数据信息化留存,便于不同岗位人员的数据共享,省去繁琐的人员相互提供纸质数据;
传统食品企业的食品生产质量安全控制数字化转型流程
1、明确目标和愿景
- 确定企业数字化转型的目标:例如能提升生产效率、提升供应链管理效率、加强生产过程质量控制、改善客户体验等;
- 制定长期愿景,了解数字化转型对企业发展的战略意义,帮助企业改善依靠人为经验的生产工艺,全面提升企业全流程的管理过程,让每一环节的数据不再孤立;
2、评估现状和需求
- 对现有生产工艺和过程记录情况进行全面评估,识别痛点和问题,根据HACCP要求,对现有生产线和生产过程控制关键控制点进行分析,确定需要使用的物联化传感器和系统预警提醒方案。
- 分析企业现有的数据记录方式和情况,确定需要更换的记录软件和增加的记录内容。
3、制定数字化战略和规划
- 基于目标和评估结果,制定数字化转型战略,确定各工序段需要采集信息化记录的人员;
- 制定详细的数字化转型项目规划,包括时间表、人员需求、预算和风险评估等;
4、选择合适的硬件和系统
- 对现有生产工艺和过程记录情况进行全面评估,识别痛点和问题,根据HACCP要求,对现有生产线和生产过程控制关键控制点进行分析,确定需要使用的物联化传感器和系统预警提醒方案。
- 分析企业现有的数据记录方式和情况,确定需要更换的记录软件和增加的记录内容。
5、实施和培训
- 开展数字化转型项目,包括系统安装、物联化传感器的配置和集成等。
- 线下对各环节工序段的操作人员进行培训指导,并根据实际反馈优化流程和采集方式;
6、数据采集
- 实际生产过程中的数据采集完整性、共享性,以及各数据分析展示情况;
- 整合不同系统和数据源,实现数据的共享和一致性。
7、流程优化
- 正式启动企业数字化采集系统,并进行持续的监测和管理;
- 收集和分析数据,进行业务指标跟踪和评估,优化系统和各流程采集方式等;
8、持续改进和创新
- 建立一个持续改进和创新的方式,鼓励一线员工提出改进建议和创新想法;
- 定期审查数字化转型的成果,并根据反馈和新技术趋势进行调整和改进;